Pathways to Operational Excellence – Part 1
- Richard Blow
- Apr 20, 2020
- 3 min read
Updated: Aug 5, 2021
No one is an island, and no BPI methodology in isolation is a silver bullet

While everyone currently is focused on short term issues including cash flow, when things start to return to normal the focus for business leaders will quickly shift to 'what have we learned from this', 'what changes do we need to make to our business in response to this' or ' what so we need to do now to get quickly back on our feet?'.
As we move towards this upswing, it may seem tempting to jump straight to a business improvement methodology such as Lean, Six Sigma or TOC. However without having the fundamentals in place, implementing these methodologies in isolation may yield only temporary and sub-optimal results. Why is this?
This article focuses on an essential business tool that is often being skipped over by businesses in their haste to achieve competitive advantage, and why this tool is essential for accelerating and sustaining operational excellence and business growth.
A fundamental step in achieving operational excellence is the establishment of a ‘best practice’ business operating system. More commonly known as Management Operating Systems (MOS), they are essential to ensure that substandard outputs are continuously identified and actioned.
Many businesses have implemented at least some MOS principles to help achieve Operational Excellence. MOS implementations can be lengthy and complicated and often includes substantial cultural change, but it doesn’t have to be difficult! Most best practice professionals believe it is not possible to achieve and sustain Operational Excellence without applying MOS and PDCA principles, many businesses unfortunately believe that they can bypass this step.
MOS systems incorporate essential business operations procedures including best practice planning, execution, control and review. These systems were originally developed by the likes of Unilever, Colgate Palmolive, Proctor and Gamble, as well as Toyota. While in recent decades, development of electronic media and IT tools have streamlined the application and output of these systems, the core principles have remained the same as the fundamentals for operating an effective and efficient business have not changed..
Anyone familiar with the Toyota Production System (TPS) knows that a stable business operating platform based on Plan-Do-Check-Act (PDCA) principles is essential for all the other business improvement initiatives stacked on top of this platform to be effective.
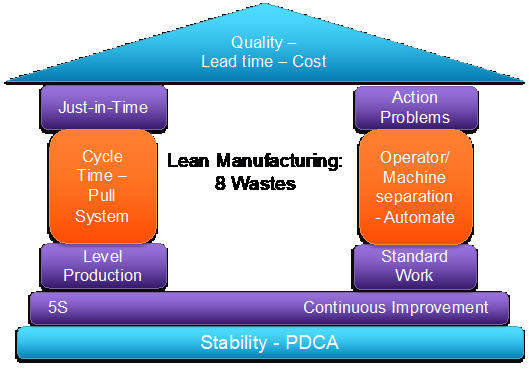
A MOS is built around the fundamentals of PDCA principles and it is always the first continuous improvement tool that a business should implement, as it creates the transparency required to immediate identify substandard performance anywhere in the business’ operations. Applying PDCA principles to all parts of the business’ operations also ensures that all subsequently implemented improvement methods become more effective and sustainable
Once a robust MOS is in place, the introduction of Lean, Six Sigma or TOC into your business as usual (BAU) becomes the natural next step.
With the ongoing development of Enterprise Resource Planning (ERP) systems, selected MOS type functionality has been introduced to businesses in recent years through Manufacturing Execution Systems (MES). MES systems typically form the execution layer between ERP systems and PLC data retrieval systems in factories.
MES systems allow manufacturers to introduce PDCA principles, the key requirement to achieve Operational Excellence, to the execution part of the production process. It can facilitate superior production scheduling and execution efficiencies by creating clear and detailed real-time visibility on all forms of waste and underutilised capacity. Because of its more limited scope, an MES can achieve good results without the time, resource and change management input required to install a full MOS.
Management Operating Systems and/or Manufacturing Execution Systems are mandatory items if a business wants to achieve sustainable improvements. Part 2 of this series will go into detail about the application, similarities and differences between MOS and MES
Thank you to our Grey Haired Guru, Alex Van Ravenswaaij for his contributions to this blog.
留言