Lean and Industry 4.0
- Performance Drivers Pty Ltd
- Jun 1, 2018
- 4 min read
Updated: Aug 5, 2021
The cyber-physical era is upon us
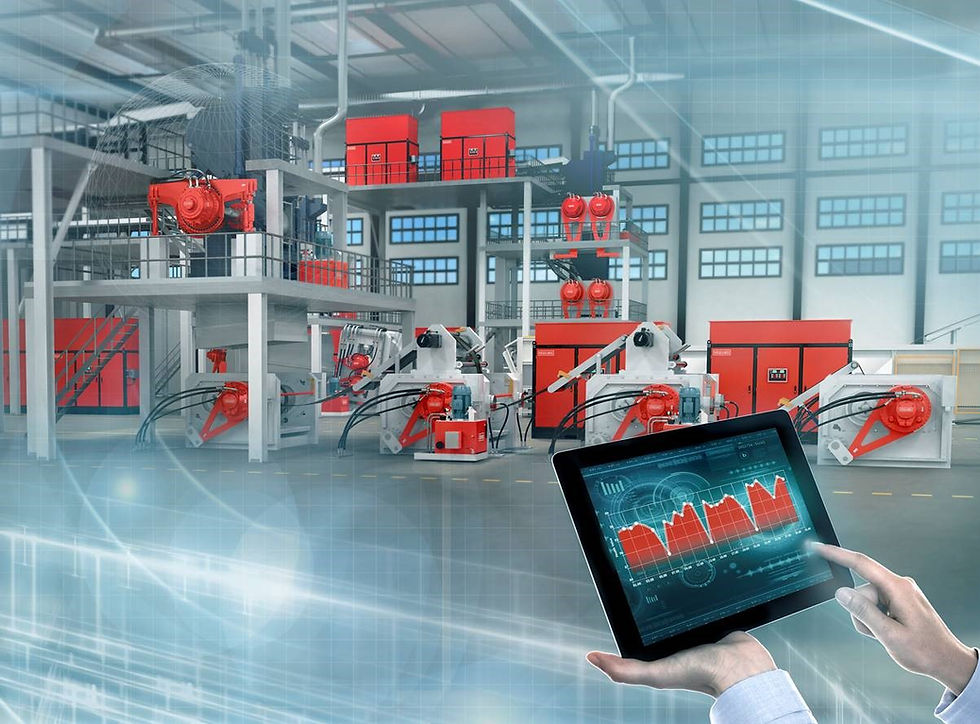
Source: Bosch Rexroth
If cloud computing, the Internet of Things, real-time sense-and-response technologies, cloud-based services, big data analytics, robotics, artificial intelligence, 3D printing and other technologies could facilitate Lean manufacturing– would you ignore them?
“Taiichi Ohno may not have mapped out an IT infrastructure that incorporated predictive analytics and closed loop feedback channels with customers, but that doesn’t mean he wouldn’t embrace them now if he were updating his concepts for today’s manufacturer,” writes Robert Hart, publications editor for TRACC a value chain improvement solution provider. It’s easy to agree that the the innovator who drove Toyota’s process improvement methods would embrace new improvement opportunities.
How Lean and Industry 4.0 fit together
There is uncertainty about what Industry 4.0 will bring and a widely held regard for Lean’s ability to improve productivity and decrease costs.
While displacing Lean to use Industry 4.0 instead has been canvassed. This view has been tempered by the evolving nature of Industry 4.0, and recognising technology is part of solving efficiency problems. The emerging consensus is to maintain the benefits of Lean and simultaneously leverage Industry 4.0 technologies to overcome the limitations of current systems.
“Industry 4.0 can be integrated in Lean Production and beyond that improve Lean Production by increased integration of ICT.”
Kolberg and Zuhlke
Voices in industry are calling for a Lean with Industry 4.0 approach.
”Discussions going forward need to be more inclusive and integrated. More Lean and Industry 4.0, rather than Lean versus Industry 4.0.” says Peter Anthony, CEO at automotive parts manufacturer UGN Inc.
“We shouldn’t make sweeping changes in our process based on data alone, so it is important to maintain our lean manufacturing perspective alongside forward-looking Industry 4.0 intelligence,” says Anthony.
In the Bosch Connected World Blog, Stefanie Peitzker says “At Bosch, our recipe for sustainable success is to build on the tried and true and combine it with innovation. Lean production represents the tried and true and Industry 4.0 looks toward the future and therefore innovation.”
Digitally enabling the lean enterprise
Industry 4.0 can enable Lean. After all, the provision of management information is critical to Lean manufacturing. And the web-based digitalisation and automation of Industry 4.0 will deliver and use information to manage processes and their connections within factories and beyond with sales, suppliers, distribution, and customers.
In the Journal of Industrial Engineering and Management, Sanders, Elangeswaran, and Wulfsberg tease out the correlation between Lean manufacturing and Industry 4.0. Looking at the current challenges in implementing Lean and finding solutions in Industry 4.0 technologies, which are summarised in the table below.

Understanding how to take advantage of Industry 4.0, or how to use it with Lean is the first step.
There is reason to pause for thought. During the 1990s and into this century many CRM system implementations failed to deliver benefits. The lessons learnt which apply to Lean production environments applying digitalisation are:
be certain it will solve a business problem and the root causes of the problem, increasing efficiency and adding value which contributes to KPIs
optimise processes before automation, automate to further optimise them, overcoming non-digital limitations
don’t employ automation as a tool to change or control worker behaviour, focus on how data and automation can empower them to be more effective
Discussions among senior leaders in construction, automotive, aerospace, electronics, materials and printing sectors identify it is pertinent to consider the implications of:
Industry 4.0 technologies connecting the operational factory environment with the world outside, particularly customers, offers significant potential to understand and respond to customer’s needs more precisely.
new data sources and predictive analysis tools providing forward-looking insight compared to the backward-looking measurement of performance most in use at present.
Start thinking about Lean with Industry 4.0 opportunities
Industry 4.0 technologies offer radical new options for a Lean production environment. New sources of data, new types of decision-making information, new connections for better communication, and cyber-physical system to advance to higher levels of value to customers and competitiveness.
To start thinking about the opportunities in your business consider these questions:
Where would better communication, information flow or real-time information flows make a difference – reducing decision-making time for production planning and control, reducing machine downtime, or connecting processes through the value stream more effectively?
What gaps and inefficiencies could be bridged with the automation of manual work?
What problems do you have in your highly optimised processes which are resisting being solved, could an Industry 4.0 technology help?
Which processes need to be optimized further before applying automation?
Could safety be improved by automating processes or using sensors to provide warnings?
Would automation of the Lean tools you use be beneficial?
Is it going to be more efficient to buy or build the capabilities to address any of the opportunities you identify to use Industry 4.0 technologies with Lean?
What will your existing IT infrastructure support, what would need to be added or upgraded? - data networks, data storage, devices, systems, and security for an Internet and data enabled production environment.
What risks do you see in any of the opportunities you have identified?
And, of course, as you generate ideas consider how employees should be involved and the implications for workplace culture.
Take advantage of Industry 4.0 technologies
The interplay between Lean and Industry 4.0 provides new ways to optimise flow through the entire value stream. From end-to-end there is an increasing range of technologies to help anticipate or predict issues and overcome them or react and fix them faster.
Businesses which have embraced Lean and have active Lean programs are well positioned to leverage Industry 4.0. With a good handle on their value streams and a culture of continuous improvement Industry 4.0 technologies present opportunities to make big improvements, getting customer’s attention and contributing to the bottom line.
For a closer look at Industry 4.0, when and where the term was first coined; 9 pillars of 4.0 and the greatest challenges lying ahead, follow this link to a recent article published by INSTRKTIV.
Bibliography
Dennis Kolberg and Detlef Zühlke, Lean Automation enabled by Industry 4.0 Technologies. IFAC-PapersOnLine 48-3 (2015) 1870–1875. https://www.sciencedirect.com/science/article/pii/S2405896315005984
Adam Sanders, Chola Elangeswaran , Jens Wulfsberg Helmut-Schmidt-University, Institute of Production Engineering (Germany). Industry 4.0 Implies Lean Manufacturing: Research Activities in Industry 4.0 Function as Enablers for Lean Manufacturing. Journal of Industrial Engineering and Management JIEM, 2016 – 9(3): 811-833 – Online ISSN: 2013-0953 – Print ISSN: 2013-8423 http://dx.doi.org/10.3926/jiem.1940 )
Comments